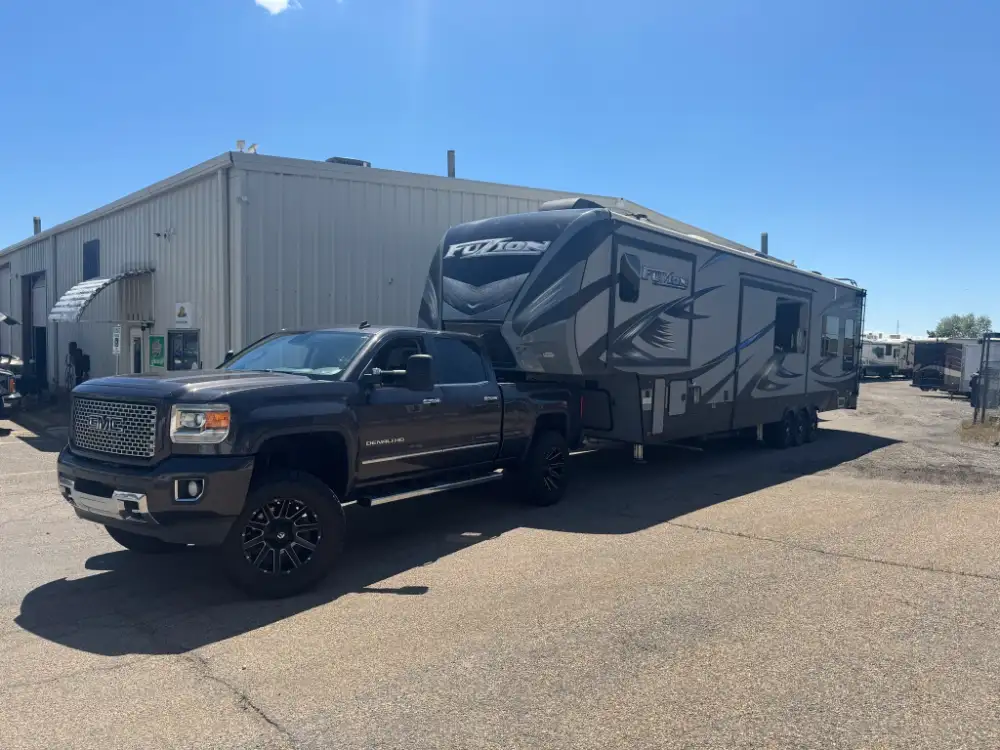
Understanding the condition and performance of your vehicle’s braking system is vital for ensuring both operational safety and longevity. Among the many components that require regular monitoring, the ZF parking brake often goes overlooked. Yet this critical device plays an indispensable role in vehicle security and stability. Whether you’re operating commercial trucks, industrial vehicles, or buses equipped with ZF driveline technology, recognizing signs of wear and maintaining a strict inspection routine can prevent severe mechanical failures and safety risks.
What Is a ZF Parking Brake?
Before diving into wear indicators and inspection practices, it’s essential to understand what a ZF parking brake is. ZF Friedrichshafen AG, a German manufacturer renowned for its innovative transmission and driveline technologies, designs parking brakes that integrate seamlessly into the drivetrain systems of heavy-duty and commercial vehicles. Unlike traditional manual parking brakes, the ZF parking brake is typically part of an integrated electronic or hydraulic system, often located on the output shaft of the transmission or within the axle assembly.
The design ensures robust holding force, capable of securing vehicles even on steep inclines. This makes them particularly well-suited for buses, trucks, and construction equipment. Because ZF systems are engineered for durability and precision, any sign of degradation must be taken seriously. Failure to maintain a ZF parking brake can lead to unintended vehicle movement, drivetrain damage, or catastrophic brake system failure.
Early Signs of Wear: Knowing What to Look For
Detecting early signs of wear on a ZF parking brake can be challenging without a keen eye and a solid understanding of its operational characteristics. One of the most immediate signs is increased pedal or lever travel. If the brake feels “loose” or requires more movement than usual to engage, it may indicate pad wear or a decline in hydraulic pressure. Unusual noises, such as grinding, clicking, or high-pitched squeals during engagement, are another red flag. These sounds can suggest internal friction, worn components, or contaminated brake surfaces.
Visual inspection may also reveal clues. If you notice excessive brake dust, metallic debris, or uneven wear patterns on the pads or discs, it’s a strong indicator that internal components are deteriorating. Fluid leaks near the actuators or hydraulic lines can compromise brake pressure and effectiveness, pointing to seal or hose wear.
Moreover, some advanced ZF systems may trigger dashboard warning lights or diagnostic codes when the parking brake malfunctions. Ignoring these alerts can result in more extensive damage and costly repairs down the line.
Performance Decline: Consequences of Ignoring Wear
When signs of wear go unaddressed, the performance of the ZF parking brake can degrade rapidly. One of the most dangerous consequences is brake slippage. In commercial or industrial applications, this can result in a parked vehicle unexpectedly rolling away, endangering nearby personnel, infrastructure, or cargo.
Another concern is uneven engagement. This occurs when the brake does not apply force uniformly across the system, leading to one side of the axle or drivetrain absorbing more stress than the other. Over time, this asymmetry can damage the differential or transmission output, increasing the likelihood of mechanical failure.
Heat buildup is another symptom of a deteriorating brake. As friction materials wear down and internal components work harder to maintain holding force, thermal stress can warp brake rotors or overheat hydraulic fluid. This not only diminishes the brake’s effectiveness but also compromises the surrounding driveline components.
In some cases, worn parking brakes can create a domino effect across the braking system. For example, if the ZF parking brake is part of an electronically controlled brake system (ECBS), its malfunction can cause faults in related subsystems, such as automatic braking or load distribution modules.
The Importance of Scheduled Inspections and Preventive Maintenance
Given the critical role that a ZF parking brake plays in vehicle safety and functionality, regular inspection is not just advisable—it is essential. Industry best practices recommend that commercial vehicle fleets integrate brake system checks into their routine maintenance schedules, typically every 5,000 to 10,000 miles, depending on usage intensity and terrain.
A proper inspection of a ZF parking brake involves both visual and functional assessments. Technicians should check for pad thickness, rotor condition, actuator response time, and the integrity of hydraulic or electronic connections. Diagnostic tools can be used to access the vehicle’s onboard control unit and scan for any fault codes or irregularities in performance metrics.
Lubrication of moving parts, recalibration of sensors, and software updates (in electronically controlled systems) are also part of a comprehensive maintenance protocol. By maintaining these practices, fleets can ensure consistent brake performance and prolong the lifespan of the ZF components.
Preventive maintenance also offers substantial economic benefits. It is far less costly to replace worn pads or leaking actuators during a scheduled service than to face unexpected downtime due to a total brake failure. Moreover, demonstrating diligent maintenance can be a compliance requirement for many transportation authorities, reducing liability risks during audits or inspections.
Long-Term Benefits and System Longevity
The long-term benefits of regular inspection and timely repairs extend well beyond immediate safety improvements. By ensuring that your ZF parking brake remains in optimal condition, you support the overall health of the vehicle’s driveline and reduce strain on associated systems. This results in fewer unexpected repairs, lower operating costs, and enhanced vehicle resale value.
In fleet operations, well-maintained parking brakes contribute to higher vehicle uptime and more predictable maintenance scheduling. This reliability translates into operational efficiency, especially for businesses that rely on tight delivery schedules or heavy machinery operations.
From a sustainability perspective, prolonging the life of mechanical components reduces the need for replacements and lowers the environmental impact of manufacturing and disposing of automotive parts. Furthermore, it demonstrates a commitment to responsible fleet management, which can strengthen customer trust and brand reputation.
The ZF parking brake, while often less visible than other components like the transmission or engine, is a cornerstone of vehicular stability and safety. Treating it with the same level of attention and care ensures that your vehicles remain compliant, efficient, and above all, safe.
Conclusion
Understanding what a ZF parking brake is and recognizing the early signs of wear and tear can prevent significant issues down the road. Regular inspection and maintenance are crucial not only for safety but also for the longevity of your vehicle’s braking and driveline systems. Whether you’re managing a commercial fleet or operating a single heavy-duty vehicle, investing time in monitoring your ZF parking brake pays dividends in performance, safety, and peace of mind.
Need Vehicle Maintenance Near You?
Start your next adventure with confidence—reach out to us at Rocky Mountain RV & Service today! Whether you’re prepping for the open road or gearing up for rugged UTV trails, our expert team in Layton, Utah is here to deliver the maintenance and care your vehicle needs. From comprehensive 45-point RV inspections and slide-out RV services to suspension, clutch, and shock repairs for UTVs, we do it all—quickly, reliably, and affordably. We take pride in getting you back on the road and keeping you exploring without hassle. Visit our website or give us a call now to schedule your service—we can’t wait to help you hit the road again!